Light Box Construction for a
TeleVue NP101 4 inch Refractor
By Michael R Turner
I will not rehash the necessity of
taking flat frames to cleanup CCD images. There are many articles
scattered around the internet that provide a very in depth discussion of
this topic. My preference is Ron Wodaski's The New CCD Astronomy,
Chapter 6, Increasing Image Quality (http://www.newastro.com).
The construction is based on the
ideas from Dean Salmon (http://galaxies.com/ccdinfo/LightBox.aspx) and
the 5k Ohm pot from Don Goldman (http://astrodon.com/LearningCurve.html).
I added my own modification of the tube supports so that the Light Box
would be free-standing on the telescope.
Parts List
1. 1 sheet of X-Acto Foam Board - 5 mm thick.
2. 4 White LEDs Radio Shack 276-320 (D1 - D4)
3. 4 LED Panel Mounts Radio Shack 276-080
4. 1 5K Ohm Linear Taper Pot Radio Shack 271-1714
(R2)
5. 1 Knurled Knob Radio Shack 274-424 (for pot)
6. 1 100 Ohm 1/4 watt resistor (from resistor kit)
(R1)
7. 2.5 mm monaural audio jack (12vdc receptacle)
(J1)
8. 185 cm cord with 2.5 mm monaural stereo plug
installed (12vdc feed)
9. 2 sheets of Translucent Alabaster velum paper
10 Hold-The-Foam Foam Board glue.
Tools
1. X-Acto knife
2. Dremel Tool with Saw Blade cutting Wheel
3. Steel Ruler 455 mm
4. Hot glue gun with clear glue
5. Soldering iron
6. Hand tools
7. Glue stick
The Circuit Design
The LEDs are white LEDs that are formed by doping a blue
LED with yellow phosphor. They are rated at 3.6 vdc forward voltage at
20 ma with 1100 mcd luminous intensity. The viewing angle is
approximately 100 degrees at the 50 percent viewing points on either
side of center. I chose the panel mounts to simplify recovering the
LEDs if I decide to change the design. The circuit design and the LEDs
were tested to insure that they would provide the proper brightness for
the flat fields for the refractor and the ST2000XM camera. Power is
provided via a 2.5 mm monaural audio jack (12vdc receptacle) installed
in my main power pack (battery case).
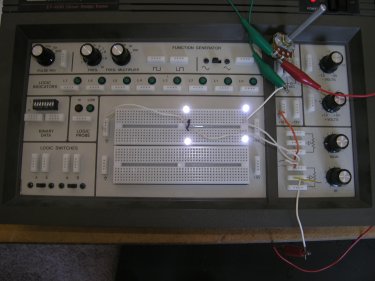
1. LED circuit
2. Testing the LEDs
Getting Started
I chose the 5 mm foam board because I have experience
working with this material (good old story boards from marketing
class). Using the proper techniques can result in precise cuts and
clean edges. It is very light weight, and structurally sound, once
glued together. The main design modification was to add an additional
67 mm to the rear of the light box and include a second circular tube
support so that the box would be self-standing on the telescope. The
basic box is 280 mm by 175 mm by 175 mm. Using Dean's formula of 2
times the objective diameter for the length of the box, the interior of
the box is 202 mm by 165 mm. I cut three 165 mm square pieces using an
X-Acto knife for the front piece and the two internal supports, two 175
mm by 280 mm pieces for the top and bottom, and two 165 mm by 280 mm
pieces for the sides. The NP101 has a built-in dew shield with an
outside diameter of 125 mm, but also has a tapered nose. Using the lens
cap from the refractor as a template, I cut a 122 mm hole in one support
and a 126 mm hole in the rear support using the Dremel tool with the
circular saw blade.
3. Tube support template
4. Cutting tube supports
The tube supports were dry fitted to the scope and minor
adjustments were made.
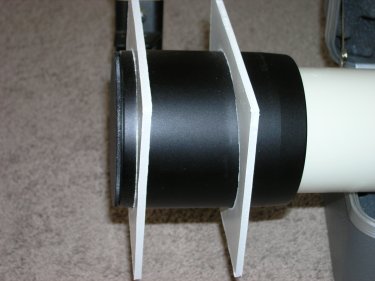
5. Tube supports
6. Checking tube support fit
Construction
I glued the two 165 mm by 280 mm
side pieces to the front 165 mm square piece using the Hold-The-Foam
glue. This glue has a 15 second initial setup time, but also allows you
to readjust the pieces before it fully cures in about 2 minutes. The
Hold-The-Foam glue is available at many Art’s and Craft’s stores. I
glued one of the 175 mm by 280 mm pieces to the sides and front to form
the bottom of the box.
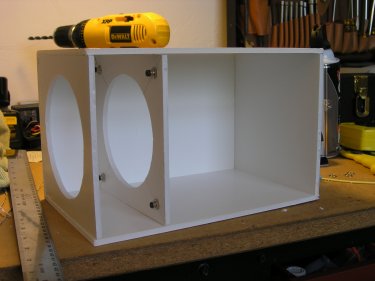
7. Basic Box
8. Box with Tube Supports
Mounting and Wiring The LEDs
The internal support with the 122 mm hole is used for the
LED holder. Using the centering guide marks left over from the laying
out the circles, I marked and drilled 4 – 6 mm holes 32 mm from the edge
of the circle for the LED mounts. The nuts for the LED mounts just fit
the 5 mm thickness of the Foam Board if the lock washer is removed.
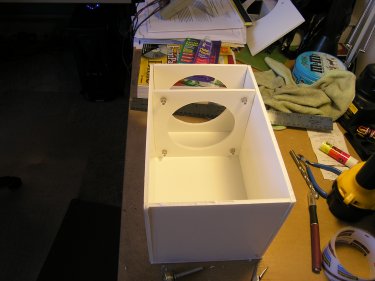
9. LEDs Mounted - Rear View
10. LEDs Mounted - Front View
The LEDs are wired in series, with a 100 Ohm fixed
current limiting resistor and a 5,000 Ohm linear taper potentiometer, to
allow adjusting the brightness of the LEDs, also in series on the
positive supply side. The LEDs are “bare”. They do not have a
diffusing cover. The 12vdc power receptacle and the 5K Ohm pot are
mounted in the Foam Board using the hardware that came with the items.
The knurled knob was mounted on the shortened 5K Ohm pot shaft and
secured with its set screw.
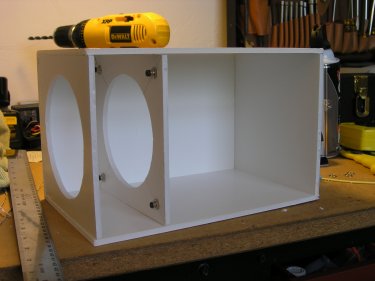
11. LED Wiring
12. Basic Box with Internal Tube Supports
The internal tube support, with the LEDs, was glued in
place 101 mm from the inside of the front of the box. I made two
measurement marks on each side of the box 106 mm from the front to
insure that the support was straight. I was careful not to make any
marks on the inside of the main light box. Next, the outer tube support
with the 126 mm hole was glued in place at the rear of the box.
Finishing the Construction
At this point, I did a dry fit of the box on the
telescope to verify that all of the parts cleared the tube and that the
internal support fit the tapered dew shield nose properly. It fits
approximated half way up the taper. The velum paper was then glued in
on all sides. This paper eliminates the harsh reflections caused by the
glossy Foam Board and the shadows created by the bare LEDs. The result
is well mixed and diffused light. Finally, the top was glued to the
box. This was probably the hardest piece to get squared. Fortunately,
the care measuring and cutting the other pieces was worth the effort.
First Light (pun intended)
The 12 vdc power cord was made from an old wall power
pack cable and a 2.5 mm monaural audio plug. The 185 cm power cord
provides enough cable to fit any angle that the mount may slew the scope
to. I do not leave the cable connected while the mount is slewing. I
turned on the computer, turned on the ST2000XM and verified that they
were working. The light box was turned on and CCDOPS was used in the
Focus mode to adjust the brightness of the LEDs to approximately 30,000
units, which is about 67 percent of the full well capacity of the
ST2000XM. Several flats were taken and analyzed to “see” what the
optical system looked like.
13. First Light
14. Initial Flat Frame
Finishing the Light Box
The prototype of the box works well. There are several
light leaks that must be fixed, where the glue did not completely seal
the gaps. Also, an outer covering needs to be installed to shield the
box. It looks like a big orange flame stuck on the end of the
telescope.
Conclusion
Building the light box was fun and educational. Future
modifications include modifying the LED circuit to wire the LEDs in
parallel to provide a finer range of brightness adjustment. And, change
the LED mounts to use a diffuser over the LEDs.
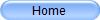
|